Polyimide’s Role in Electronics: Applications and Process
Explore polyimide’s applications and processability in electronics, showcasing how it enhances performance and reliability across various industries.

Polyimide is a high-performance polymer used extensively in electronic components due to its superior thermal stability, electrical insulation, and potential for survival in harsh environments. Because of its flexibility and strength; hence, it is highly required in areas such as flexible printed circuits, insulation of wires, and semiconductor packaging. The contribution of polyimides is significant, in a broad range of applications from electronic manufacturing to aerospace components.
Key Properties of Polyimide for Electronics Applications
Property | Specification | Industrial Relevance |
---|---|---|
Thermal Properties | 400°C continuous | Component assembly, Reflow |
Operating Range | -269°C to 400°C | Aerospace/Military use |
Dielectric Strength | 280 kV/mm | Circuit insulation |
Insulation Resistance | 10¹⁶ Ω·cm | Safety critical systems |
Flexural Strength | 231 MPa | Flexible electronics |
Bending Endurance | >200k cycles at 180° | Foldable devices |
Chemical Stability | Class H (IPC) | Manufacturing processes |
Moisture Absorption | <1.3% at 85% RH | Humid environments |
Dimension Stability | <0.1% at 200°C | Precision electronics |
UV Resistance | >5000 hours | Outdoor applications |
Applications of Polyimide in Electronics
Flexible Printed Circuits (FPC)
Due to its excellent flexibility, thermal stability, and resistance to wear and tear, polyimide is commonly used in flexible printed circuits. In compact devices like smartphones, tablets, and medical devices, these circuits enable a balance between reliable performance and design flexibility.
Wire and Cable Insulation
In wire and cable applications, polyimide acts as an insulating layer when these applications operate in harsh or high temperature environments. Its high dielectric strength makes it effective insulation in high voltage systems, automotive electronics or industrial equipment where it is required that the equipment is durable and performs well in extreme conditions.
Semiconductor Packaging
Polyimide films protect sensitive components from environmental stressors, such as heat, chemicals and mechanical impact, in semiconductor packaging. Microelectronics application option for its high temperature tolerance and electrical insulation properties which allow small size without compromising reliability.
Display Technologies
In display technologies, polyimide is used for its flexibility, it allows the production of OLED and LCD displays with flexible substrates. This property has enabled foldable screens and wearable devices to be developed. The clarity and thermal stability of polyimide keep visual performance and durability in compact and high resolution displays.
Aerospace Electronics
Polyimide is used in aerospace applications for electronics exposed to the most extreme conditions, such as intense heat to radiation. Robust insulation for wiring, circuit boards, and sensors used in spacecraft and aircraft provides consistent performance in high altitude, high vibration, and high-temperature environments.
Polyimide Processing Method
Film Formation
Casting Polyamic Acid precursors onto a substrate, and thermally curing the resulting films form durable polyimide films. The high temperature stability and electrical insulation required from electronic applications help make this film forming method ideal for producing thin, flexible layers for use in flexible printed circuits as well as insulation.
Coating Techniques
The polyimide is placed on a substrate by various coating techniques, which include spin coating, dip coating, spray coating, etc. The coatings protect electronic components from harm by the environment: electric insulation and chemical resistance. Each method is chosen according to thickness and consistency requirements: spin coating is employed for high precision, thin films and spray coating for wider applications.
Photolithography Compatibility
Polyimide’s compatibility with photolithography makes it a fine patterning material of choice for semiconductor manufacturing. Selective exposure of polyimide layers to UV light, followed by development, allows the construction of intricate circuits and microscale features. This compatibility makes polyimide particularly suited for microelectronics, where precision and minimization are of highest importance.
Thermal Curing Process
Polyimide films are applied to perform thermal curing, a process where film is heated to a specific temperature to convert polyamic acid to polyimide. This curing is then used to increase the stability, mechanical strength and thermal resistance of the material. The properties are optimized with very careful control of the process parameters, such as temperature and time, and the material is thus suitable for demanding electronic applications.
Challenges in Processability
Handling High Temperatures During Processing
For curing, polyimide needs high temperatures, which are difficult to manage and can damage both the substrate and properties of the final material. Make sure that your heat is distributed evenly to avoid warping, or uneven curing for precision applications. It is often necessary to have advanced equipment and maintain quality and performance with careful temperature control.
Adhesion to Different Substrates
Polyimide may exhibit poor adhesion to many substrates, such as metals, ceramics, or other polymers, because of different surface properties and thermal expansion rates. It may also result in poor adhesion and delamination or reduced durability. To overcome this, bonding is often improved by application of surface treatments or primers, increasing the reliability of the material in complex assemblies.
Precision in Thin-Film Applications
For thin film applications such as flexible printed circuits and semiconductor packaging, precise film thickness control is needed for Polyimide applications. Thickness variations may change electrical insulation, flexibility and overall performance. But even though processing techniques such as spin coating and photolithography are optimized for thin films, they do not provide uniformity, particularly for microscale applications.
Manufacturing Considerations
Process Temperature Requirements
It is often necessary to process polyimide at high temperatures to achieve its best properties. Temperature control and consistency are necessary, manufacturers must use equipment capable of handling these temperatures. Both heat settings and adherence to recommended temperatures are important to be properly monitored.
Handling and Storage
Polyimide material is highly sensitive to environmental conditions such as exposure to humidity and UV. They must be stored in a temperature-controlled environment and normally in moisture resistant packaging to prevent premature curing or degradation.
Quality Control Measures
Ensuring polyimide quality through rigorous testing is important. Common quality control for this regard includes an investigation into the thickness of the film, adhesion strength, dielectric properties, and thermal stability. Advanced imaging and testing techniques have been used to catch defects in an early stage of manufacturing, such as microscopy on thin films and tensile testing on flexibility.
Bottom Line
Polyimide has played a crucial role in the development of electronics because of its unparalleled strength and flexibility in extreme applications. Fixing the processing difficulties will unleash its potential for modern innovation in high-performance, future-ready electronic devices.
If you are not familiar with Polyimide material, but need some Polyimide Parts/components for your project. UVTECO, as a leading supplier of Polyimide, will be the best partner, because we stock Polyimide Sheet, Rod and machine it according to your drawings.
Related Blogs
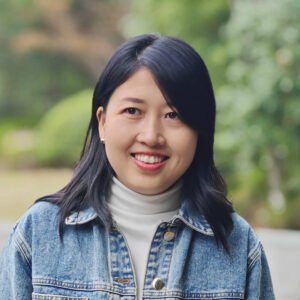
Looking for a trustworthy Supplier
Need a Trustworthy Supplier of Plastic, Foam, Sponge, Rubber, Metal, and Machining Solution. Click the Button, We Will Be In Touch With You As Quickly As Possible.