ABS plastic, or ABS, also known as Acrylonitrile Butadiene Styrene, is a crucial construction material in numerous industries like automotive, electronics, medical devices, etc.
Professionals, engineers, and product designers highly favor this material for its unique blend of properties like durability, impact resistance, excellent moldability, and many more. However, to maximize the potential of ABS, it is essential to make this remarkable plastic.
Machining ABS plastic demands precision, skill, and a deep understanding of the material’s characteristics. Here, we detail the process of machining ABS plastic along with the associated advantages. We also detail the addressing approaches related to chip management, heat management, etc.
Advantages of Machining ABS Plastic
Before knowing the ABC machining process, it is essential to understand the respective competitive advantages.
In-depth Exploration of Machining ABS Plastic
In this section, we detail various machining methods of ABS plastic depending on design requirements, preferences, and needs.
Molding Process of ABS Plastic
The following are the stepwise approaches.
- Step 1: First, we design the required outcome. First, we consider the workpiece’s thickness to be consistent. Second, in the design, we include ribs or radii to boost strength and prevent snapping. Third, we maintain a ratio of radius to wall thickness of not less than 0.3 for optimal stress reduction. Finally, we do not use larger radii in the design process to avoid shrinkage issues.
- Step 2: We start to melt the ABS plastic at 180-230°C. Here we avoid ABS’s exposure to higher temperatures to prevent material degradation. In this stage, we also reduce the moisture content to 0.05% or less from the initial range of 0.2% to 0.4% before ABS plastic molding.
- Step 3: Now, we determine the injection pressure of ABS plastic inside the mold in consideration of its viscosity.
- Step 4: In this step, the melted ABS plastic is injected through the mold’s opening under controlled temperature and pressure. In general, we impose high pressure here.
- Step 5: It is time to leave the formation for a while to allow it to cool down.
- Step 6: Once the newly shaped ABS becomes cool and solid, it is extracted from the mold.
- Step 7: Finally, we examine the outcome’s quality carefully. If there are any uneven or irregularities in the formation, we repair them using sandpaper or polishing substances.
Machining of ABS Plastic Using CNC
The following is the step-by-step guideline.
- Step 1: In the first step, we decide on the design of the final component of ABS plastic. Then we create the design on computer-aided design software.
- Step 2: During this phase, we carefully input all the parameters of the design component, like depth, radius of the curves, threading intervals, etc. In the milling process of ABS by CNC machining, the insertion of correct parameters is essential to ensuring precise final results.
- Step 3: In the CAD environment, depending on ABS plastic’s brand and quality, we set V cutting speed: typically within a range of 980 to 1640 feet per minute. We also set the rotational speed at 2000 RPM depending on the solid status of the plastic. However, the selection of speed depends on the specific design of the end product. For instance, we go for a lower work speed when deeper holes or intricate curves are needed.
- Step 4: In this step, we decide on tool selection. In general, depending on work criteria and specific requirements, we select appropriate tool sizes: ranging from 1/8″ flat-end mills to 1/64″ flat-end mills. Here, we carefully examine whether the selected tools will suit the set feed rates, spindle speeds, and cutting depths. Below are the two prominent tool sets for milling ABS plastic using a CNC machine.
Tool size (1/8″ flat end mill): The standard feed rate is 1500 mm/min, spindle speed of 16,400 RPM, and a maximum pass length of 1.27 mm.
Tool size (1/64″ flat end mill): The standard feed rate of 762 mm/min, spindle speed of 16,400 RPM, and a maximum pass length of 0.254 mm.
and a maximum pass length of 0.254 mm. If the tool size is incompatible with the pre-setted and rotation speeds, then those need to be adjusted on the software. Finally, we use carbide or high-speed steel tools. - Step 5: Following this, the workpiece of ABS is accurately positioned within the milling machine. Here, it is essential to mount the workpiece precisely.
- Step 6: After initiating the machine, we carefully observe the work progress. This phase involves two crucial responsibilities: the consistent extraction of debris and using coolant to effectively control heat generation.
- Step 7: After completing the task, we employ fine-grit sandpapers to achieve a smooth and polished finish on edges, curves, etc.
Tips on Machining ABS Plastic
Below are some crucial tips for machining ABS.
- Ensure that the minimum wall thickness of the ABS workpiece is 0.5 mm to prevent warping issues.
- In consideration of the cutting depth, it is required to go up to ten times the diameter of the tool bit.
- Use a single flute tool to ensure smooth chip clearance.
- Working with ABS material often causes skin irritation, so thorough hand cleaning is essential.
- The use of coolants is important to deal with heat generation.
Final Words
Our guide on the process of machining ABS plastic is helpful for professionals, product designers, etc., from various industries. By employing the mentioned guidelines, one can do ABS machining effortlessly and easily. However, we always suggest professionals wear standard personal protective equipment to avoid encountering any unwanted happenings.
Related blogs
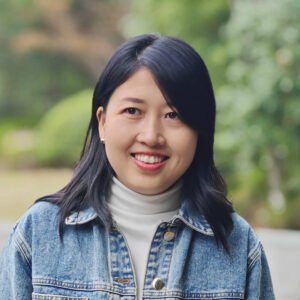
Looking for a trustworthy Supplier
Need a Trustworthy Supplier of Plastic, Foam, Sponge, Rubber, Metal, and Machining Solution. Click the Button, We Will Be In Touch With You As Quickly As Possible.