Mastering the Art of PET Injection Molding
Explore the best practices for PET injection molding, including troubleshooting challenges and perfecting techniques for consistent, high-quality output.
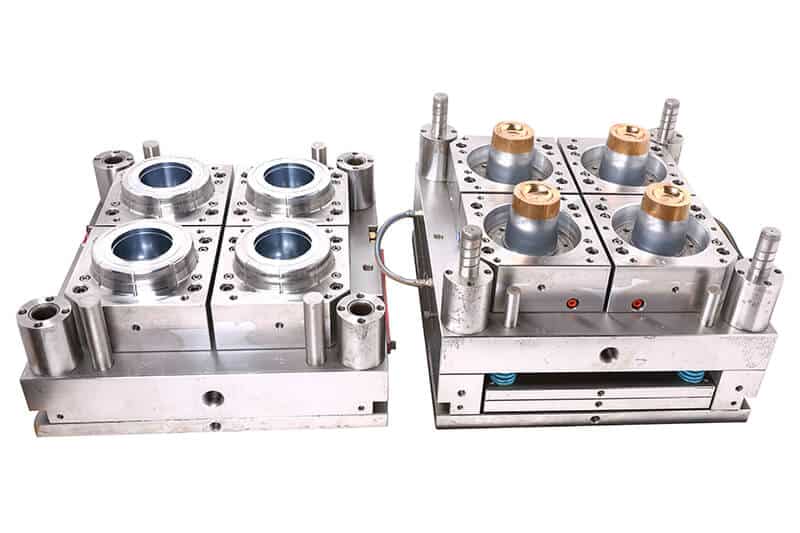
The PET injection molding process requires a certain level of proficiency, understanding, and creativity in order to manufacture good-quality PET products. It helps to shape PET material to shape different forms like from water bottles to automotive parts. By mastering the process, manufacturers can produce durable, lightweight, and precise plastic parts to meet diverse needs.
Understanding PET Materials Properties
PET material, or polyethylene terephthalate plastic, is amongst the most used thermoplastics in the manufacturing industry. Many PET variants can utilize other than producing drink bottles and are extruded into sheets, rods and tubes then machined into fine parts. With injection molding, the manufacturers can mold PET to make various products. However, It’s necessary to comprehend its chemical and physical characteristics to conduct a successful injection molding process.
Chemical and Physical Characteristics
PET has many chemical and physical characteristics that make it suitable for creating high-quality product parts. Here are some of the PET’s unique properties in detail.
Property | Value/Description |
---|---|
Chemical Formula | (C₁₀H₈O₄)n |
Monomer | Ethylene terephthalate |
Polymerization | Condensation polymerization |
Molecular Weight | 30,000 – 80,000 g/mol |
Crystallinity | Semi-crystalline (20-40% achievable) |
Density Amorphous | 1.33 – 1.37 g/cm³ |
Density Crystalline | 1.45 – 1.51 g/cm³ |
Glass Transition Temperature | 69 – 115°C |
Melting Temperature (Tm) | 250 – 260°C |
Thermal Decomposition | Begins around 340°C |
Specific Heat Capacity | 1.0 – 1.2 kJ/(kg·K) |
Thermal Conductivity | 0.15 – 0.40 W/(m·K) |
Moisture Absorption | 0.1 – 0.2% |
Thermal Expansion | 60 – 80 × 10⁻⁶/K |
Oxygen Permeability | 0 – 40 cm³·mm / (m²·day·atm) |
CO₂ Permeability | 100 – 130 cm³·mm / (m²·day·atm) |
Volume Resistivity | 10¹⁵ – 10¹⁶ Ω·cm |
Surface Resistivity | 10¹³ – 10¹⁶ Ω/sq |
Chemical Resistance | Acids, alcohols, oils, and some solvents |
Refractive Index | 1.57 – 1.58 |
Why PET is Ideal for Injection Molding
Here are some of the key reasons that make PET a suitable material for injection molding:
Excellent Formability
PET’s molecular structure allows it to mold easily in different shapes. As it flows easily through injection molding manufacturers can create complex designs while maintaining dimensional accuracy and precision.
Versatility
PET’s versatility and dimensional stability allow it to mold complex and intricate parts with accuracy while maintaining quality with minimal distortion.
High Resistance to Heat and Chemicals
PET has a melting point of 250 – 260°C and it is resistant to several chemicals that gives it the ability to be molded at high temperatures without deformation and losing its integrity.
Key Steps of the PET Injection Molding Process
Here are the key steps of the PET injection molding process
Clamping
In the clamping stage, two halves of mold hold together under high pressure so they remain closed during the injection process. The clamping force prevents material leaks out and helps to maintain product shape.
Injection
The PET material has been dried and melted and is then forced under high pressure into the mold cavity. The PET is melted and conveyed through a nozzle that fills the cavity completely with the polymer. The injection pressure must be controlled very closely in order to get the material into the details of the mold and especially in complex shapes of the part.
Dwelling
The pressure needs to be maintained in the molten PET even after filling the cavity. The dwelling stage ensures that the mold is completely filled and shaped with accurate dimensions and precision.
Cooling
Then, the PET materials need to be cooled to solidify. The cooling stage is essential as it will impact the strength and stability of the final product. The cooling time can vary depending on the materials grade, part thickness and design.
Mold Opening
This step prepares the molded part for removal. The mold opening must be done in the right time to allow the part to solidify before it is ejected out of the mold. If the mold opens too early, the product would have distortions, if it opens too late, it will affect the production cycle.
Ejection
The finished PET part is pushed out of the mold with the aid of ejector pins. The part is now ready to undergo any post processing or even packing.
Advantages of PET Injection Molding
Durability and Strength
The PET injection molded products have high durability and strength. For high tensile strength this material can’t be easily broken and therefore very suitable for packaging and consumer products.
Clarity and Transparency
One of the major qualities of PET material known to possess outstanding optical quality. The correct molding makes the PET products to resemble glasses that is why it is popular for production of containers for beverages, food items, cosmetics, and other consumable goods packaging.
Recyclability
PET is among the most recycled plastic polymers globally. Therefore, PET injection molding products can be easily collected and used again in the production of new material thus reducing the amount of plastics that may end up in the environment.
Challenges in PET Injection Molding
Material Degradation
PET is highly sensitive to moisture, and if the material is not dried before injection, it can face hydrolytic degradation during the molding process. Such conditions can create weak and fragile products.
Injection Defects
Poor control of the process parameters causes formation of injection defects like warping, voids, sink marks and short shots. Therefore, it is possible to have the molded parts being aesthetically or functionally defective.
Cycle Time Optimization
Cycle time includes the one molding cycle of the clamping, injection, dwelling time, cooling time, mold opening and ejection. Long cycle time directly decreases productivity and increases manufacturing costs.
Applications of PET Injection Molding
Packaging Industry
Packaging industry is the largest consumer of PET injection molding. Because of its high transparency, mechanical strength and good barrier properties. It is well suited to packaging applications including beverage bottles and food containers.
Consumer Goods
PET injection molding is also used in the production of different consumer products like household items and electronic devices for its impact strength, flexibility and appearance.
Industrial Applications
PET injection molding is used in the industrial sector to make parts that need strength, chemical resistance, and accuracy. Some of the applications include manufacturing automotive parts and electrical and mechanical parts.
Wrapping Up
PET injection molding is among the most innovative manufacturing methods. Its mechanical characteristics, combined with versatility in diverse sectors, make PET plastic one of the most reliable materials for manufacturing high-quality, resistant components.
UVTECO is a leading supplier of PET injection molding and PET parts in China. If you have any questions, contact us now!
Related Blogs
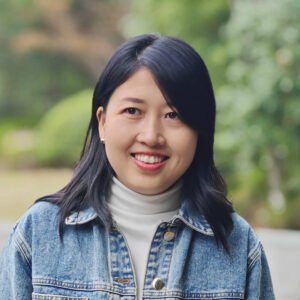
Looking for a trustworthy Supplier
Need a Trustworthy Supplier of Plastic, Foam, Sponge, Rubber, Metal, and Machining Solution. Click the Button, We Will Be In Touch With You As Quickly As Possible.