PEEK Plastic Injection Molding – An Engineer’s Guide
Get all expert tips for PEEK plastic injection molding! Learn how to create strong and detailed plastic parts for different uses in this helpful guide.

PEEK is a high-performance engineering thermoplastic that is always in high demand for a wide range of applications. However, some applications require intricate designs or specific shapes, and that’s where effective injection molding comes in.
Due to the excellent friction resistance, mechanical strength, and thermal properties, PEEK can be easily processed in the molding process. Even the best part is that effective injection molding techniques offer a unique way to create stronger PEEK plastic parts.
This guide will explain all the suggestions to consider in the PEEK injection molding process and help you avoid common mistakes.
What is Plastic Injection Molding?
Plastic injection molding is a special manufacturing process in which high pressure is used to create molded products. The process melts, injects, and gives the plastic a specific shape for various applications, such as automotive, medical, or other.
The complete molding process demands some parameters, which should be tightly maintained to ensure the quality of the plastic component. This method is perfect when you need to mass produce products with specific shapes for various applications, for example PEEK Gears, PEEK Bolts, PEEK Nuts, etc.
Things to Consider for Successful PEEK Plastic Injection Molding
Before you begin the PEEK thermal molding process, here are some key considerations you should know about:
1. Choose High-Quality PEEK Raw Materials
For effective molding with PEEK, choosing the right material truly matters. Though PEEK features all high-grade physical and chemical properties, still choose the purest form of PEEK.
It should have the highest elongation and toughness. Go for carbon filler PEEK, which is stronger than steel PEEK and 7% lighter than glass fiber.
2. PEEK Injection Mold Design
While injection molding, proper design guidelines for PEEK are a must to make PEEK parts easier to manufacture. It also reduces the cost and prevents possible defects. Here are some needed guidelines for PEEK injection molding design:
Design Aspect | Guideline |
---|---|
Wall Thickness | Use 1.0 to 3 mm thickness. Make sure to keep it even. |
Radii | Avoid sharp edges. Use a curve that is 25% of the wall thickness. |
Draft Angle | Use 0.5° to 2° angle for easier removal from the mold. Smoother parts require less angle, whereas complicated parts need more. |
Part Tolerance | Unfilled PEEK shrinks 1-1.8%, and filled PEEK shrinks up to 0.9%. So, pick the mold size as per the shrink accordingly. |
3. Maintain Cleanliness
You must be cautious of any type of contamination when you are dealing with PEEK. Most other plastics can’t handle the high heat needed to mold PEEK and could break down. So ensure properly cleaned ovens and machines before injecting PEEK material.
How to Injection Mold PEEK Plastic?
Injection molding PEEK plastic requires careful planning and attention to detail. Follow these essential steps to ensure successful molding:
Step 1: Select the Right PEEK Material
The complete injection molding is a complex manufacturing process. To get success here, first, you have to ensure the right PEEK resin for your specific application.
This is important because each application demands a different grade of PEEK materials. For this, you can go through a quick test to ensure in this instance.
Step 2: Prepare Your PEEK Pellets and Injection Molding Machine
The next step is preparing your PEEK pellets and injection mold. PEEK granules are typically dry. However, they can absorb water from the air. So, before using it for injection molding, you need to make sure it’s really dry. For instance:
When done, check the PEEK injection molding machine. The molding machine barrel should be clean. You can run a heat-stable purging compound through the machine. It will remove any leftover materials from previous use. Next, you have to choose the gate size.
Step 3: Mold Temperature and Speed Setting
Before the injection process, two essential factors you need to consider are:
1. Mold Temperature
PEEK has high processing temperatures that range from 350°C to 400°C. So you have to keep your mold temperature at least that high to make sure all the final parts turn out well. Insufficient temperature can cause quench-cooling issues in PEEK parts.
2. Injection Speed
While using the mold machine, you may find silver streaks near the gate of molded parts. This is the sign that the screw spins too fast and gases or moisture get trapped in the plastic.
For this, you need to maintain a balanced pressure. The mold pressure can be as high as 20 bar, and reducing it can make the mold hotter and inject the plastic faster.
Step 4: Load PEEK Resin
The next part is loading the PEEK resin into the mold. Remember, PEEK is a semi-crystalline polymer. That means it has a structure that can easily shrink when it cools compared to amorphous thermoplastics.
To solve this issue, you should choose the gate size to be at least two-thirds of the maximum thickness of the part.
Step 5: Start the Injection Molding Process
Do a quick check to ensure there are no clumps or contaminants in the material. If so, start the injection molding cycle. You have to monitor the process closely to ensure that the material flows correctly. Load extra material into the cavity to ensure that it is filled.
Step 6: The Cooling Cycle
It is an important phase when you have done the injection molding. If the product is thick, it needs much time to cool down.
During this time, if it comes into contact with cool air too fast, the shape of PEEK products can be damaged. For this, you should not go through a rapid cooling process.
What are the Advantages of PEEK Injection Molding?
There are a number of reasons highlighting PEEK as a superior thermoplastic choice for injection molding. Here is a quick glimpse:
Advantage | Description |
---|---|
Biocompatibility | Medical-grade PEEK is inert and safe for implants |
High-Temperature Resistance | With a melting point of 343 °C, PEEK can easily maintain itself in extreme temperatures. |
Low Offgassing | PEEK doesn’t release trapped gas at high temperatures, which is best for sensitive applications. |
Wear Resistance | PEEK is a highly durable and low-friction material. You can use fillers like carbon fiber to enhance the strength. |
Strength and Rigidity | PEEK offers excellent mechanical properties. It ensures that it withstand mechanical stress and produces robust parts in molding. |
Conclusion
PEEK Plastic is a perfect engineering plastic that can be used in high-temperature and chemical environments. Therefore, it is not easy to make it through the injection process.
UVTECO is an expert in PEEK Plastic in China. We have a lot of projects with PEEK Plastic Injection Molding. If you are looking for a trustworthy supplier of PEEK components/parts through an injection molding process, Contact UVTECO, for a suitable solution for your project.
Related Blogs
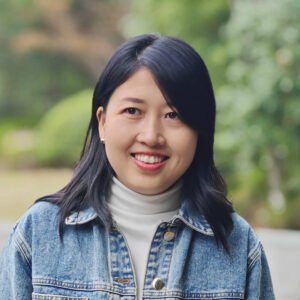
Looking for a trustworthy Supplier
Need a Trustworthy Supplier of Plastic, Foam, Sponge, Rubber, Metal, and Machining Solution. Click the Button, We Will Be In Touch With You As Quickly As Possible.