Machining UHMW Plastic: A Complete Guide
Explore the ultimate guide to UHMW plastic machining. Elevate your skills for seamless fabrication.
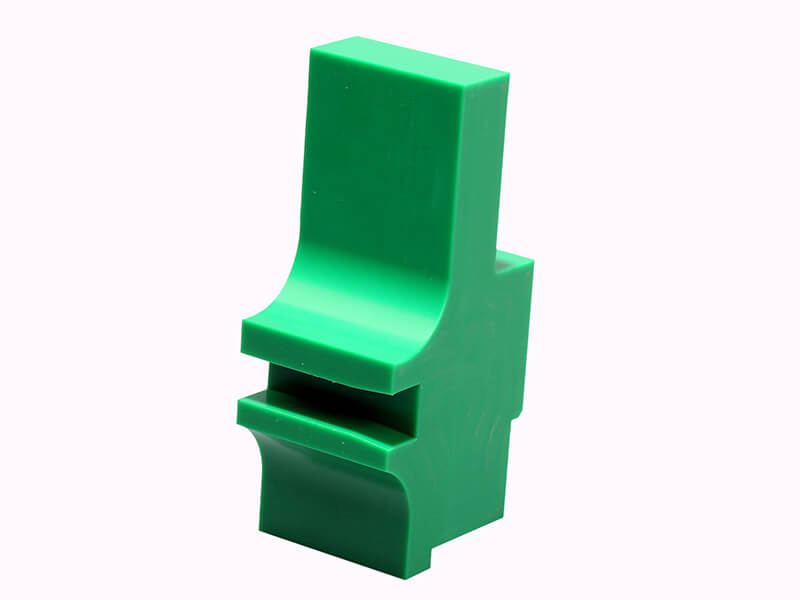
Thermoplastic polyethylene includes ultra-high-molecular-weight polyethylene (UHMWPE or UHMW). It is also called high-modulus polyethylene (HMPE), and its molecular mass is usually between 3.5 and 7.5 million AMU. It has very long chains. The longer chain helps the polymer backbone carry more weight by strengthening molecule bonds. This creates a solid material with the best impact strength of any thermoplastic.
UHMW Material and Properties Options
Machining Parts of UHMW Plastic
When UHMW polyethylene is used to make parts, it has a great mix of fantastic qualities.
UHMW has high abrasion resistance, a low coefficient of friction, self-lubrication, a surface that doesn’t stick, good chemical fatigue resistance and impact resistance, is easy to machine, and has good noise-dampening qualities. It has many great qualities, like being very resistant to wear and damage and working well at very low temperatures (like liquid nitrogen, which is -259 degrees C). When the temperature reaches 185 degrees F, UHMW will soften and lose its ability to fight wear.
Because UHMW expands and contracts a lot when the temperature changes, it’s not a good choice for close-tolerance applications in these environments.
But Vanderveer Industrial Plastics’ CNC machining skills make it easy to create custom UHMW parts with tight manufacturing tolerances.
Process of Machining UHMW Plastic
As part of our plastic machining services, we cut, turn, shape, mill saw, anneal, and do other things to the plastic. We use automation for jobs that are done repeatedly and need to be done perfectly and consistently, no matter how many there are. This ensures the form, size, length, and so on are correct.
The problem comes from the fact that UHMW has a low melting point (270°) and a high COF (120 x 10″ IN/IN/ÜF). Our machining process for UHMW plastic:
Limit heat
It’s essential to keep heat from building up for the best results. The machining itself creates friction, which leads to heat. When heat builds up, it changes how things are measured, and the cutting tool can turn into a “melting tool.” Think about these ways to avoid this problem:
To drill:
Cutting and milling
Sawing
Speeds and feeds
Cooling agents
Contamination
Contamination is a significant worry when machining polymer parts for highly technical fields like aerospace and medical sciences. To ensure the highest level of cleanliness down to the sub-molecular level, our machining designs, heat-treats, and machine plastics are used. Any sub-manufactured metal work is done outside of our plant. This removes the chance of metals getting mixed up in the process.
Final Words
UHMW plastic is one of the most popular plastics for industrial parts. If finding a professional and trustworthy supplier of machining UHMW parts is difficult, contact UVTECO. We stock the frequently used UHMW plastic sheets, rods, and tubes for fast delivery.
Related Blogs
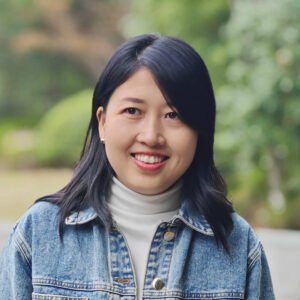
Looking for a trustworthy Supplier
Need a Trustworthy Supplier of Plastic, Foam, Sponge, Rubber, Metal, and Machining Solution. Click the Button, We Will Be In Touch With You As Quickly As Possible.