Heavyweight Performers: 7 Plastic Components with Superior Strength
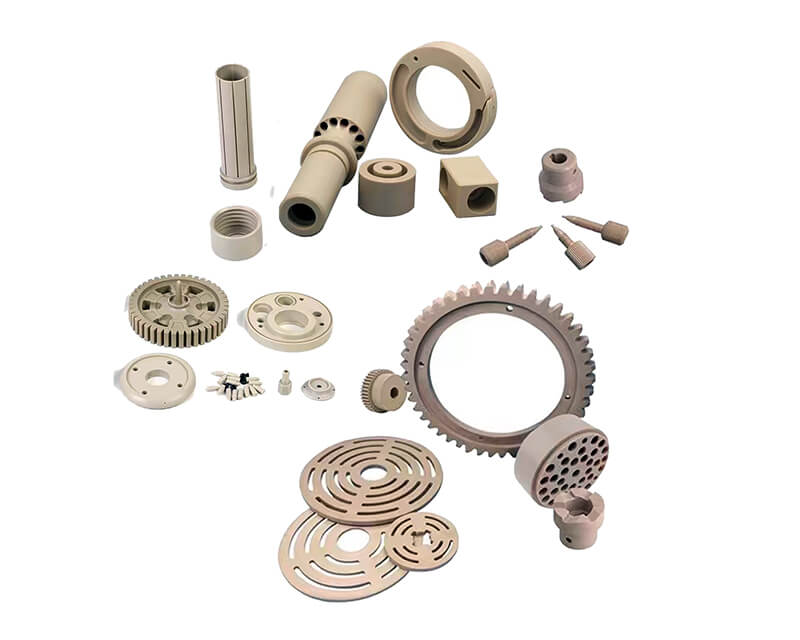
There are various types of plastics available in the market with different characteristics and features. Some are heavy, some are lightweight, some are transparent, and many more.
It is essential to know about heavy-duty plastics like PET, HDPE, Rigid PVC, PP, LDPE, PS, ABS plastic, etc. We must know every aspect of these materials to ensure perfect and precise use.
All these heavy plastics are unique with their own characteristics. And they have different applications for maximizing the usability to get the most out of these materials. Here, we elaborate on the distinctive characteristics of these items while providing effective knowledge regarding the applications.
heavy plastics:
PET
The full form of this heavy-duty plastic is Polyethylene Terephthalate. Polyethylene terephthalate is produced through condensation polymerization. In this process, chemical reactions take place between ethylene glycol and terephthalic acid.
Here, the mechanisms of polymerization consist of two primary types of polymerization: step-growth and chain-growth polymerization. It’s known for its strength, transparency, versatility, and recyclability.
Applications:
HDPE
In the search for heavy-duty plastic, we list HDPE in the second position. HDEP’s full form is High-Density Polyethylene, and it is a thermoplastic polymer. Idealistically, HDPE is the more crystalline iteration of polyethylene than the others: it is empowered by a higher degree of strength, rigidity, and toughness.
Its industrial use traces back to the 1930s; at that time, this material was used in producing radar cables during World War II. One more thing to mention here: HDPE’s thermoplastic nature is surprisingly exceptional; it can be heated to its melting point, then cooled down, and reheated, And in this process, no significant amount of deformation happens.
Applications:
PVC
Polyvinyl Chloride, commonly known as PVC, is one of the most extensively used polymers in the world. Due to its remarkable versatility, PVC is widely used in numerous industries to manufacture daily-life items.
It is considered a core material in construction, transportation, packaging, electrical and electronic realms, and even healthcare applications. This high-strength thermoplastic is produced by the process of polymerization of the vinyl chloride monomer. And by nature, it is amorphous.
Applications:
PP
Polypropylene, or PP, is another crucial addition to our list in terms of heavy plastic. First of all, its versatility is phenomenal. The associated heavy-duty nature makes it highly suitable for hard packaging, creating automotive components, medical devices, or household items; PP’s adaptability and durability are considered a blessing to modern life. And its contributions to modern life play diversified roles in shaping our world.
Finally, Polypropylene (PP) is a low-density and stress-resistant thermoplastic. In the mid-1950s, it was made from a propene (or propylene) monomer.
Applications:
LDPE
Its full form is low-density polyethylene; it is the opposite of HDPE. However, even though it contains the term “low-density,” it is capable of competing with any other top-notch heavy-duty plastics.
This thermoplastic is highly favored for its pliability, resilience, and robustness. Here, the must-mentioned distinguished feature is that LDPE showcases heightened flexibility while maintaining reduced rigidity.
Applications:
PS
Polystyrene, this synthetic polyester, can be rigid and foamed. It is renowned for its robustness, rigidity, and remarkable transparency. The production of the material includes the polymerization of styrene.
Polystyrene primarily consists of the monomer styrene; the process usually creates a homopolymer. Its classification can vary, with some types falling under “thermoplastic” while others are “thermoset.” The hinging is vitally dependent on the imposed heat on the processing endeavor.
Applications:
ABS
ABS, short for Acrylonitrile Butadiene Styrene, is a versatile and non-transparent thermoplastic polymer. ABS has a low melting point, which makes it easily recyclable. When heated, it transitions into a liquid state at around 221 degrees Fahrenheit.
ABS is a terpolymer formed by polymerizing acrylonitrile, styrene, and polybutadiene in specific ratios, typically ranging from 15% to 35% acrylonitrile, 5% to 30% butadiene, and 40% to 60% styrene. ABS was patented in 1948 and commercially introduced in 1954 by Borg-Warner Corporation.
Applications:
Final words
Heavy plastic items are now an integral part of our modern lives. These offer a remarkable blend of strength, durability, and versatility. From the automotive to construction industries, everywhere, these plastics are used enormously. However, our list of heavy plastic components will assist professionals in selecting the right construction material to produce cost-effective products.
These heavy-duty plastics play a vital role in our daily lives. Their ability to withstand harsh environmental conditions, resist corrosion, and provide cost-effective alternatives to traditional materials has made them indispensable in numerous applications.
Finally, we suggest more research and experiments on these materials to upgrade this construction material, increasing usability, suitability, and applicability.
Related blogs
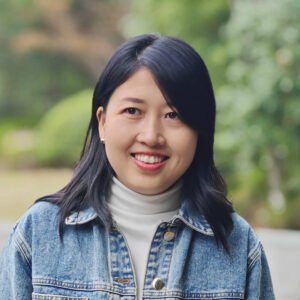
Looking for a trustworthy Supplier
Need a Trustworthy Supplier of Plastic, Foam, Sponge, Rubber, Metal, and Machining Solution. Click the Button, We Will Be In Touch With You As Quickly As Possible.