Must-Know Benefits of ABS Plastic Injection Molding
Unlock the benefits of ABS plastic in injection molding – quick insights on efficiency, precision, and design advantages for optimal manufacturing results.
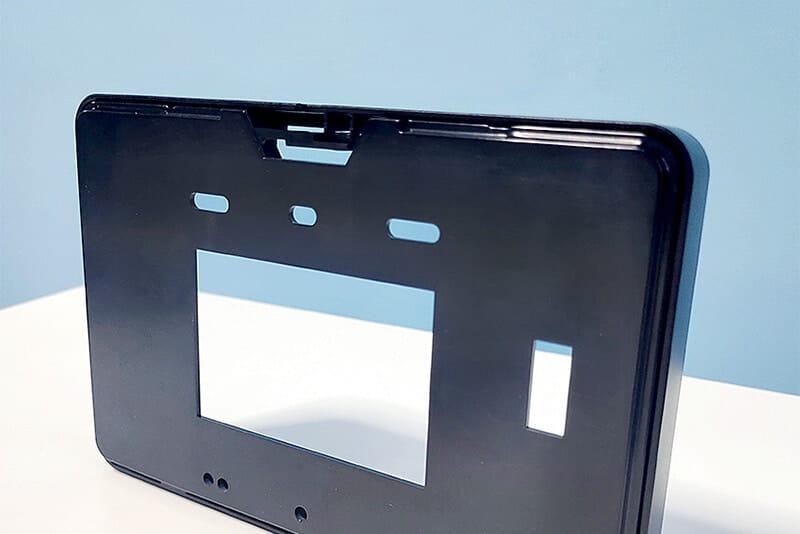
ABS plastic is a popular choice for product manufacturers when injection molding is a core requirement. The reasons behind such a high disability are low production cost, manufacturing ease, good dimensional stability, and many more. In short, the benefits of ABS plastic for injection molding are huge.
The issue is that without an in-depth understanding of ABS injection molding, availing of those benefits is nearly impossible. To embrace this context, we discuss the associated benefits, problems, systematic approaches, etc. Let’s start.
What is ABS Plastic Injection Molding
Following the mentioned term, ABS plastic injection molding refers to a specialized manufacturing process to produce plastic parts and components of Acrylonitrile Butadiene Styrene.
The injection molding process involves precisely engineering molten ABS injection into an earlier-created mold, cooling, and solidifying the molten ABS inside the respective cavity to achieve the desired shape.
Step-by-Step Guide to ABS Injection Molding
Here, we reveal our methodological approach to performing injection molding of this thermopolymer. Depending on product requirements, we choose the injection molding process from over molding, insert molding, and gas-assisted injection molding.
In-depth Discussion on Benefits of ABS Plastic Injection Molding
The following are the most essential benefits of injection molding of this polymer.
Design Flexibility
The injection molding of ABS offers a higher degree of design flexibility. This process allows us to incorporate complex designs meeting customized requirements. Here, undercut, folding, complex shaping, layer creation, etc., become very easy.
Cost Effectiveness
Cost is a crucial concern in every plastic component manufacturing process as it influences the end item price more. We have found injection molding of the considered thermoplastic is substantially cost-effective. The first reason is the low price of ABS. The second reason is that injection molding allows us to mass-produce a component within a shorter period, saving costs associated with the workforce, energy, etc.
Excellent Surface Finish
The components must retain a smooth surface and dimensional accuracy in plastic parts production. ABS’s injection molding exactly does the same. It does not host defects and imperfections, reducing the post-production tasks.
Versatility
The injection molding process of ABS offers a more significant level of versatility. This production process allows us to meet worldwide customer needs more efficiently.
Production Efficiency
Maintaining a strict deadline is always a critical term in the industrial manufacturing process. In this case, our automated injection molding of ABS ensures continuous and uninterrupted production, ensuring greater production efficiency.
Must-Know Issues of ABS Injection Molding
We understand the need to know the issues associated with plastic injection molding and discuss those here.
Sink Marks
Product outcomes hosting sink marks is a critical issue in ABS injection molding. These marks orient when the exterior layer’s solidification process runs faster than the interior. We apply proper gate design, venting, and cooling strategies to mitigate this issue.
Flash
“Flash” refers to melted ABS flowing through the mold-clamping, producing a thin layer of solid ABS on the created component. We eliminate this by applying appropriate clamping force and adjusting injection pressure.
Short Shots
Short shots are the result of the improper filling of the mold with liquid plastic. To restrict the creation of incomplete parts, we put critical concerns in gate design, temperature application, viscosity maintenance, etc.
Issue With Hygroscopic Nature of ABS
The Acrylonitrile Butadiene Styrene is hygroscopic. It hosts moisture content very quickly, creating problems in the quality of the end items. We maintain strict guidelines in the product storing process to mitigate this issue and keep the plastic pellets and components from contact with moisture.
Parts Produced Through ABS Injection Molding
The following table contains data regarding industry wise parts manufactured using ABS injection molding.
Industry | Components |
---|---|
Construction | Housings of power tools |
Automotive | Door trims, interior decorative items, HVAC components |
Consumer items | Blocks, toys, furniture |
Healthcare | Housing and enclosures of various medical devices |
Final Thoughts
Our in-depth discussion on the benefits of injection molding ABS has proven influential for professionals. All the aspects of the context mentioned above are from our practical experiences, which can act as standard guidance. Finally, our costs range from $1000-$3,000, considering the minimum order quantity, design complexity, delivery deadline, etc.
UVTECO is a leading supplier of injection-molded ABS plastic parts. If you are looking for a trustworthy supplier, please contact us.
Related Blogs
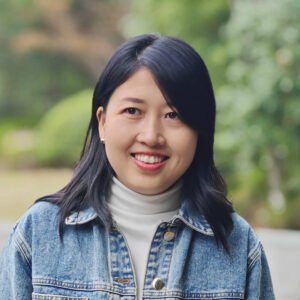
Looking for a trustworthy Supplier
Need a Trustworthy Supplier of Plastic, Foam, Sponge, Rubber, Metal, and Machining Solution. Click the Button, We Will Be In Touch With You As Quickly As Possible.