Material Processing Tips on CNC Machining FR4 and G10
Learn expert CNC machining tips for FR4 and Garolite G10, including techniques for precision, material handling, and achieving high-quality results.
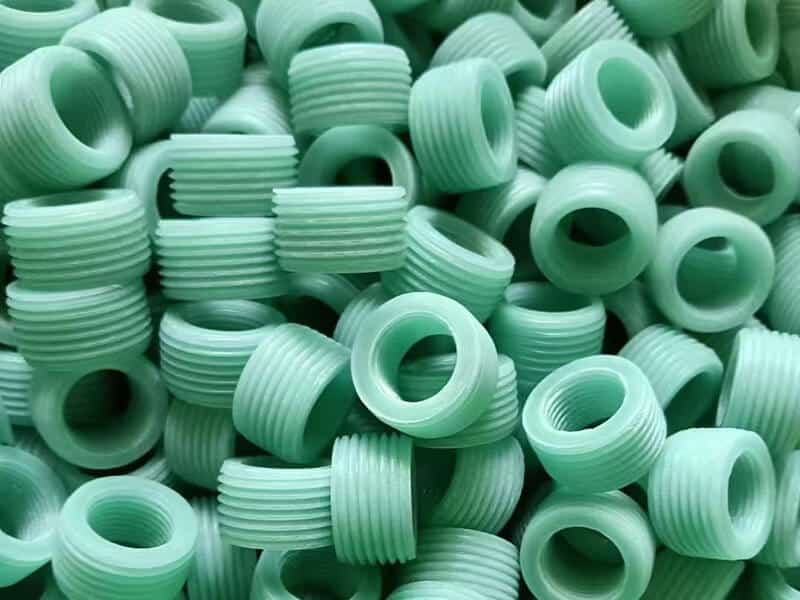
G10 and FR4 are fiberglass-reinforced laminates well-desired in various industries due to their superior properties in terms of mechanical strength, heat resistance, and electrical insulation. These two composite laminates are widely used in electronics, aerospace, automotive, etc.
Here, to make parts or components of parts for the mentioned industries using G10 and FR4, accurate precision in CNC machining is crucial. Additionally, mitigating challenges like tools ware, delamination, etc., are essential.
Following this, we would like to provide a stepwise guide for CNC machining of G10 and FR4, along with some expert tips.
Basics of FR4 and G10
Garolite Grade 10 and FR4 are composite materials formed by epoxy resin-based bonding of multiple fiber woven glasses. As per industry standards, G10’s ‘G’ represents Garolite, ‘10’ represents the grade, ‘FR’ stands for ‘fire-retardancy,’ and 4 is the grade.
Key Properties of FR4 and G10
Common Applications of FR4 and G10
G10 glass epoxy laminate is widely used to manufacture washers, terminal boards, cryogenic components, firearm components, electric items, etc. On the other hand, FR4 is used to produce printed circuit boards, aircraft components, electric insulators, turbine blades, solar panel components, and so on.
Step-by-Step CNC Machining FR4 and G10
This section details the CNC machining processes of G10 and FR4. Considering the base characteristics’ similarities, the same CNC machining process applies to both G10 and FR4.
However, in the CNC machining of Garolite 10 and FR4 glass epoxy laminate, the core differences are inherited in the tool type, feed rate, etc.
Material Preparation
In this pre-machine process, manufacturers must select the right sized, shaped, and thickened sheets or blocks of G10 and FR4 and remove the dust and other contaminants from the surfaces.
If the used G10 or FR4 sheet or block is enormous, we suggest making a pre-cut using a saw to reduce the machining time. In this step, professionals must arrange and wear standard PPE.
CNC Machine Setup
The following tasks need to be performed.
CNC Machine Feed Setting
CNC Machining Process
First, it is to be mentioned that in the overall CNC machining processes, the coolant needs to be applied to restrict excessive heat generation, aka eliminating the risks of material crake, tools’ ware, etc. The following are the machining processes of G10 and FR4.
Post-machining Process
Ending the CNC Machining Process
Challenges in G10 and FR4 CNC Machining
Expert Tips for Material Processing: G10 and FR4 Fiberglass Epoxy Laminates
With decades-long experience, our experts at UVTECO provide the following tips to enhance the effectiveness of G10’s and FR4’s CNC machining.
Conclusion
We expect that our elaboration on G10 and FR4 CNC machining in terms of material processing will help the professionals, designers, etc. enormously. There are indeed challenges associated with processing G10 and FR4, but these can be mitigated by using our recommendations.
Finally, we strongly recommend that users go to highly experienced manufacturers in the respective industry to get quality G10 and FR4 components. UVTECO is a leading supplier of FR4 and G10 sheets, rods and tubes in China, meantime, we also provide machining services. If you are looking for a trustworthy supplier, contact UVTECO now!
Related Blogs
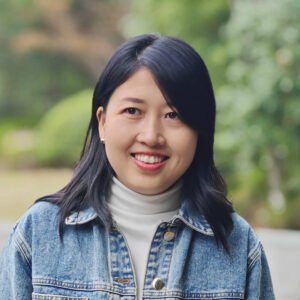
Looking for a trustworthy Supplier
Need a Trustworthy Supplier of Plastic, Foam, Sponge, Rubber, Metal, and Machining Solution. Click the Button, We Will Be In Touch With You As Quickly As Possible.