HDPE Vs. PET: Which Plastic Is Better for Your Needs?
HDPE vs PET: Compare these two plastics to see which is better for your project, focusing on strength, sustainability, and cost-effectiveness.

Most manufacturers, product designers, industry professionals, etc., face challenges in selecting the right construction materials. When it comes to creating full parts or components using plastic, the selection process becomes tougher as there are numerous types of plastics with their pros and cons.
The same goes for choosing between HDPE and PET plastics. Both are popular and lucrative construction materials that can serve similar purposes. Here, by conducting a critical comparison, we provide strategic answers to the question of which is better: HDPE or PET. Let’s start.
Basics of HDPE
HDPE, also known as high-density polyethylene, is a thermoplastic polymer invented by Karl Ziegler in 1953. Its mass use started at the end of the 19th century.
Production Process
Its production involves separating ethane from natural gas. The isolated ethane goes through ‘steam cracking’ to form ethylene gas, which is later used to create polyethylene chains through polymerization in a high-density environment with a Ziegler-Natta catalyst.
The resultant is liquid HDPE, which is later molded as per requirements and cooled down for further use.
Base Properties
Common Applications
Basics of PET
PET, also known as Polyethylene Terephthalate, is a thermoplastic polymer invented in 1945 by DuPont’s chemists. It is considered a dominant construction material in many industries, such as bottle production and synthetic fiber production.
Production Process
PET is generally produced through condensation or solid-state polymerization of ethylene glycol and terephthalic acid. Both of these chemicals are carefully purified before the reaction occurs.
Here, ethylene glycol is generated from ethylene, and terephthalic acid is obtained from an organic chemical compound named xylene. Upon getting the liquid state PET, molding and cooling give it the required shape for further use.
Base Properties
Common Applications
Critical Comparisons: HDPE Vs. PET
When comparing HDPE and PET plastics, the variables considered are durability, strength, production cost, environmental impact, degree of usability, etc.
1. Durability
With the associated molecular structures, both plastics fall in the tier-1 criterion of offering greater durability. Here, HDPE offers a higher impact and chemical resistance level than PET.
However, PET also provides these two facilities with a higher transparency and recyclability rating. Additionally, PET-made components host scratches more easily than HDPE.
2. Strength
The tensile strength of the average-type PET is 22 MPa, whereas the tensile strength of HDPE is 30 MPa. So, HDPE is comparatively more resistant to stretching and tearing. Again, the higher yield strength of HDPE allows it to withstand more load than PET before final deformation.
3. Production Cost
The average production cost of one ton of PET plastic is US $600-US $1000, and the production cost of HDPE is US $550-US $900 per ton. However, this price range is very general. The prices of PET and HDPE change regularly.
Also, production costs vary from company to company due to differences in management’s strategic decisions, raw material prices, energy costs, labor, and plant operational expenses. However, in simple words, the price of HDPE is slightly lower than PET.
4. Environmental Impact
HDPE and PET are bothersome construction materials like every other plastic due to their associated environmental impacts. These impacts include extracting natural resources as raw materials, using fossil fuel energy in production processes, transportation-related emissions, etc.
It must be mentioned that a PET-made bottle’s lifespan is 450 years. On the other hand, the lifespan of HDPE ranges from 50 years to 100 years. It means HDPE decomposes faster than PET.
5. Degree of Usability
First, concerning transparency, PET plastic is clearer than HDPE plastic. Second, HDPE is more flexible than PET, which makes it comparatively suitable for the production of parts or components of parts that require more bending and sharing. Third, the industrial use of PET recycling outputs is more popular and advantageous than the outputs of HDPE recycling.
What to Use: PET or HDPE
The following table provides a clear idea.
Plastic Type | Use For |
---|---|
PET | Packaging, containers, bottles, etc., for food and beverages |
If recycling is a must- Curbside recycling programs support PET recycling | |
Not usable where very high temperature is present | |
Transparency and clarity for product visibility | |
HDPE | Heavy-duty food containers, pipes, sockets, outdoor furniture |
Recyclable but not supported by curbside recycling programs | |
Parts of components of large parts which will encounter with various chemicals consistently | |
Where bulk packaging is required |
Final Words
We expect that UVTECO’s experts’ elaboration on which is better, HDPE or PET, will help industry professionals choose the right one. We suggest incorporating the given table to develop a general idea regarding the suitability of producing parts using each plastic.
Finally, one thing can be confirmed: both plastics are better, and the selection of a particular one is subject to management decisions, designer opinions, customer demand, final product type, price of the quote, and so on. If you are looking for a trustworthy supplier of HDPE, PET, and machining services, contact UVTECO now!
Related Blogs
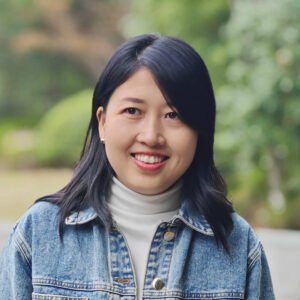
Looking for a trustworthy Supplier
Need a Trustworthy Supplier of Plastic, Foam, Sponge, Rubber, Metal, and Machining Solution. Click the Button, We Will Be In Touch With You As Quickly As Possible.