PEEK Vs. Polyimide in CNC Machining: What You Need to Know
Compare PEEK and Polyimide for CNC machining, exploring their unique properties, strengths, and applications to help you choose the best material for your project.

In manufacturing, the choice between PEEK and Polyimide for CNC machining can determine the success of your project. While both materials demonstrate great performance under extreme conditions, the two materials differ on many grounds regarding their properties and applications.
What is PEEK?
PEEK is a strong, advanced thermoplastic material with exceptional properties concerning strength, heat resistance, and chemical durability. It resists tough environments and high temperatures, up to 260°C. With good machinability and stability under stress, it is one of the top choice materials for precise, durable components in challenging applications.
Technical Specifications of PEEK
Property | Specification |
---|---|
Density | 1.30 – 1.32 g/cm³ |
Tensile Strength | 90 – 100 MPa |
Elongation at Break | 30 – 50% |
Young’s Modulus | 3.6 – 3.9 GPa |
Melting Point | 340 – 343°C |
Heat Deflection | 143 – 146°C |
Thermal Conductivity | 0.25 – 0.29 W/m·K |
Water Absorption | 0.1 – 0.5% |
Dielectric Strength | 16 – 20 kV/mm |
Chemical Resistance | Resistant to most chemicals |
Peek Applications
Medical Implants
With high biocompatibility and resistance to sterilization, PEEK enables such implants as spinal cages and dental implants and other medical devices which need permanence inside an organism.
Automotive Components
PEEK is used in gears, bearings, and sealing rings that, due to chemical resistance and good thermal stability, ought not to deform under friction, chemicals, and high temperatures.
Electrical Insulators
With excellent dielectric properties and high thermal resistance, PEEK is used in connectors, cable insulation, and other components needing electrical insulation under harsh conditions.
What is Polyimide?
Polyimide is a high-performance polymer with superior thermal stability, maintaining above 400°C without losing structural integrity. It does not show any deformation or chemical degradation under extreme conditions, which is common in usual thermoplastics. The molecular structure of polyimide provides extraordinary rigidity, very low outgassing, and low thermal expansion, making it a uniquely optimal choice for advanced technical applications.
Technical Specifications of Polyimide
Property | Specification |
---|---|
Density | 1.42 – 1.47 g/cm³ |
Tensile Strength | 85 – 95 MPa |
Young’s Modulus | 2.5 – 4 GPa |
Melting Point | Does not melt (Thermal stability up to 400°C) |
Heat Deflection | 250 – 300°C |
Thermal Conductivity | 0.12 – 0.14 W/m·K |
Water Absorption | 0.3 – 0.4% |
Dielectric Strength | 150 – 200 kV/mm |
Chemical Resistance | Resistant to most chemicals |
Coefficient of Thermal Expansion | 20 – 30 x 10⁻⁶ /°C |
Polyimide Applications
Electronics
The electrical insulation properties of polyimides make them widely used in electronics, especially in flexible PCBs where flexibility and reliability are required. The material is appropriate for designing high-quality electronic devices.
Aerospace
Aerospace industry uses polyimide extensively due to its ability to survive high temperatures and lightweight characteristics. Polyimide wiring insulation enables safe electrical systems in high-heat environments.
Industrial Applications
The industrial sector uses polyimide in the manufacture of components in contact with extreme conditions such as high temperatures and corrosive chemicals. The applications include seals, bearings, and valve components. The mechanical strength and stability of polyimides improve machinery and equipment performance and reliability in general industrial use.
Comparison Between PEEK and Polyimide
Mechanical Strength Differences
PEEK: PEEK has high tensile strength and stiffness. Due to this, PEEK is quite apt in applications that call for structural stability under load conditions. It has a higher elongation at break, being more flexible under stress-a definite advantage in those parts that are under the impact quite frequently.
Polyimide: While polyimide also has high tensile strength, it generally exhibits a slightly lower mechanical strength compared to PEEK. However, the rigidity is excellent, and it performs well in applications requiring minimal thermal expansion or at high temperatures when high rigidity is needed.
Chemical Resistance
PEEK: It is highly resistant to a wide circle of chemicals, including acids, bases, and hydrocarbons. PEEK is reliable under conditions when contacts with organic solvents and other corrosive media are frequently expected. Polyimide: Polyimide also resists many chemicals. It is particularly tough under extreme chemical conditions, like the attack of strong acid and aggressive solvent. Also, It is often used in applications where minimum chemical reactivity is a cardinal criterion, such as semiconductor manufacturing
Machinability Factors
PEEK: PEEK has a moderate toughness and dimensional stability. That’s why it is comparatively easy to machine. You can also easily drill, mill, and turn this material to high precision.
Polyimide: Polyimide is comparatively tough to machine because of its brittleness and rigidity. Special tooling and careful handling are required to avoid cracking or surface defects.
Wear Resistance
.PEEK: PEEK has high friction and abrasion resistance. This is suitable for frictional parts such as gears, bushings and bearings as well as the moving parts.
Polyimide: Polyimide is also wear-resistant, However, it doesn’t perform like PEEK’s in high-friction applications. But its resistance to thermal degradation makes it appropriate for high-heat applications.
Which One is More Suitable for You?
Mechanical Requirements
Peek: PEEK is the preferred material if the application requires high tensile strength, impact resistance or parts that take on wear and abrasion. Under load, its flexibility also means it can bend slightly without cracking, a useful property in dynamic or load bearing parts.
Polyimide: Although polyimide is strong, it also lacks the toughness of PEEK. The rigid structure of polyimide applies to applications that require high dimensional stability with minimal expansion under thermal stress and without repetitive mechanical strain.
Manufacturing Considerations
Peek: Easy to machine with standard equipment, PEEK enables cost-effective manufacturing, especially for complex parts or large volumes. Moreover, such material properties as machinability make the material versatile in respect of prototyping and custom designs.
Polyimide: Due to the hardness and brittleness of polyimide, machining may be hard. The special tool and handling increase the cost and complexity for making complicated designs.
Industry-Specific Requirements
Peek: PEEK is commonly used in industries that require durability, including automotive, oil and gas, and medical devices. It performs well in versatile applications that don’t have extremely high temperatures or other specialty needs.
Polyimide: In niche industries like aerospace and electronics where ultra high heat, electrical insulation and chemical resistance are critical, polyamide are highly valued. The polyimide’s high cost structure is appropriate for specialized performance applications.
Wrapping Up
PEEK and Polyimide have different benefits when machining. PEEK is very durable and versatile, while Polyimide is excellent at heat resistance and stability. The right material choice ensures best possible performance for your application’s unique needs.
UVTECO is a leading supplier of PEEK and Polyimide in China. If you don’t know how to choose PEEK and Polyimide for your project or are looking for a trustworthy supplier of PEEK, Polyimide, and parts/components, contact us now.
Related Blogs
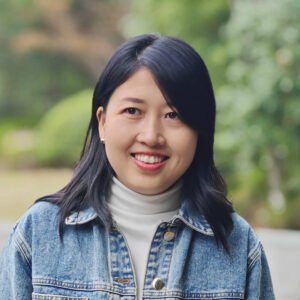
Looking for a trustworthy Supplier
Need a Trustworthy Supplier of Plastic, Foam, Sponge, Rubber, Metal, and Machining Solution. Click the Button, We Will Be In Touch With You As Quickly As Possible.