ABS Plastic Advantages in Auto Manufacturing
Explore ABS plastic advantages in auto manufacturing: enhanced durability, design flexibility, and superior performance for automotive excellence.
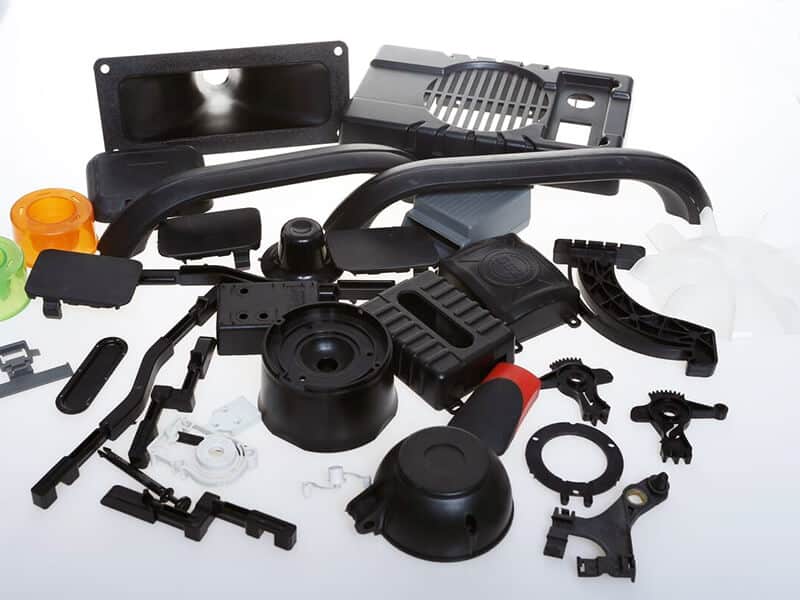
Using plastic materials for manufacturing auto parts is becoming a common practice. The versatility of complex part-making with less expense is only possible with plastic materials. However, ABS plastic is used in so many applications in the auto manufacturing industries. Here are the advantages of ABS plastics being used in auto manufacturing industries.
Why ABS plastic is best for Automotive Industries?
Here are the reasons why ABS is best for automotive industries.
Durable
There is no question about the durability of plastic products. Especially thermoplastics like ABS have a reputation for long-time durability. It is engineered with three different components that are not easily breakable. Also, it holds the integrity of the automotive parts in any environmental or chemical conditions.
Besides, ABS plastic can withstand any impact, chemical, and heat threat without deformation. Research says that ABS raisins can stay usable for more than 30 years without any cracking or breaking in a sustainable condition.
Chemical Resistance
ABS thermoplastics possess extreme levels of chemical resistance. It can withstand most common acids including aqueous acids, concentrated hydrochloric, phosphoric acids, and alkalis. In addition, this plastic has a low level of water absorption facility that makes it capable of resisting vegetable and animal fat with mineral oils.
Impact Resistance
When a car manufacturing company thinks about using a material for their product, they think of the impact resistance capability. Because it is important to ensure the performance of the car while coming in contact with other cars, uneven roads, unwilling conditions, or in an accident.
The more impact resistance feature will not only save the car from crashing but also reduce the post-impact consequences. In that case, ABS provides top-notch impact resistance features without any doubt.
Strong
Though ABS thermoplastic is not the strongest plastic ever to exist, its sturdiness is suitable for vehicle manufacturing. However, ABS plastic provides good-quality tensile strength and shock or vibration resistance. That means car parts that are made of this thermoplastic will provide strong and long-lasting durability.
Lightweight
As we know ABS is made with acrylonitrile, butadiene, and styrene components. Those three components exhibit low density when mixed up together. That is the reason behind the lightweight future of ABS plastic. Though this plastic material is low in weight, it provides good quality of non-breakable tensile strength.
Heat Resistance
Heating is a common scenario for a vehicle. Because the vehicle might not be in a shady place instead of a public parking lot. So, UV rays or the sun’s glare will easily cause heating issues for car parts. In that case, ABS plastic provides good-quality heat resistance. So, the car parts that are made with ABS will not fade in heat and lose their integrity.
Multicolor Comfortability
Multicolor features of the ABS increase the useability in different types of cars. Therefore, this plastic has different colours with the same integrity. So, manufacturers can use it in any desired application without painting with another colour. Overall, it ensures the versatility of the ABS plastic.
Sound Proof
ABS plastic is sound-proof by birth. When the three different components are mixed, they are formed into one material by heating. The melting changes the material chip’s shape and blocks all kinds of noise transmission. So, using it in the automotive industry makes it easy to soundproof the vehicle.
Scratch Resistance
The raw ABS thermoplastic doesn’t have good scratch resistance capability. But with applying primer coating, it can be super scratch-resistant. On the other hand, ABS plastic provides a good finish after primer coating. So, the surface of the part will be shiny and silky by default. That is another reason why ABS plastic is used in the automotive industry.
Easy Manufacturing
The low melting point makes the ABS plastic suitable for recycling and converted into new formation. However, this material is easy to use in the manufacturing process. Because the machining of this thermoplastic is quite easy for the low melting point. You can create any complex shapes with a simple molding method.
ABS Manufacturing Process for the Automotive Industry
Here are the popular methods for ABS plastic that are used in auto manufacturing.
Injection Molding
Injection molding is one of the best and most used machining processes for plastic materials. In this method, melted plastic will be injected into a pre-designed mold with high thermal pressure.
Then the mold will be coolant so that the melted plastic can get the integrity and density. After that, the desired product will be ready. However, the automotive industry requires custom and complex plastic parts. Injection molding makes it happen with minimal material waste.
3D Printing
3D printing is the future of the manufacturing process. It has uncountable possibilities with plastic parts manufacturing. However, 3D printing of vehicle parts is becoming popular for its versatility and usability. Shortly, this manufacturing process will rule the plastic product manufacturing industry.
Popular Automotive Applications of ABS Thermoplastic
Here are some most common vehicle parts that are made with ABS plastic.
Vehicle Bumper
The bumper is one of the important parts of a vehicle. It secures the driver and the passengers in the event of collisions. So, using ABS plastic will reduce the chance of deformation, cracking, and falling apart for its impact, and shock resistance feature.
Outer & Inner Handels
Every regular car has four doors that have two handles each. Those handles are exhibited style and used for door opening and closing. The lightweight but durable and strong plastic ABS is perfect for those handles.
Car Dashboard
Dashboards are one of the important parts of a car. But this part withstands wear and tear contact daily from the drivers and passengers. That is why ABS plastic is best for this component as it is impact-resistant, wear-resistant, lightweight, and strong.
Decorative Stripes
ABS decorative stripes not only increase the aesthetic appeal but also provide protection. On the other hand, it weighs lower than other plastic strips.
Vehicle Fenders
ABS-made fenders protect the wheels from mud, debris, and rocks while running. The properties of ABS plastic make it suitable for vehicle fenders.
Interior & Exterior Trim
Plastic materials are always the best option for exterior and interior rims. ABS plastic provides good-quality impact resistance, ductility, sturdiness, aesthetic enhancement, and durability.
Center Control Station
Complex automotive parts like the central control station are made with ABS plastic for their durability, strength, and impact-resistance features.
Under-Hood Components
Using ABS plastic sheets on under-hood components is a common practice. The properties of ABS plastics are impact-resistant, heat-resistant, and chemical-resistant making it suitable for under-hood component dress-up and custom covers.
Conclusion
The manufacturing industry is changing day by day. Modern technology like CNC opens a wide range of machining possibilities with metal and plastic materials. In this article, we have explored the advantages of ABS plastic in auto manufacturing.
UVTECO is a leading supplier of ABS plastic and machining services in China, you need a ABS Plastic Part or have questions about ABS Plastic, contact us now!
Related Blogs
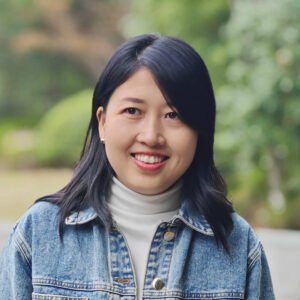
Looking for a trustworthy Supplier
Need a Trustworthy Supplier of Plastic, Foam, Sponge, Rubber, Metal, and Machining Solution. Click the Button, We Will Be In Touch With You As Quickly As Possible.