Difference Between PVDF Vs. PTFE: Which Material is Right for You?
Learn how PVDF and PTFE differ in properties, uses, and performance to help you make an informed decision on the best material for your application.
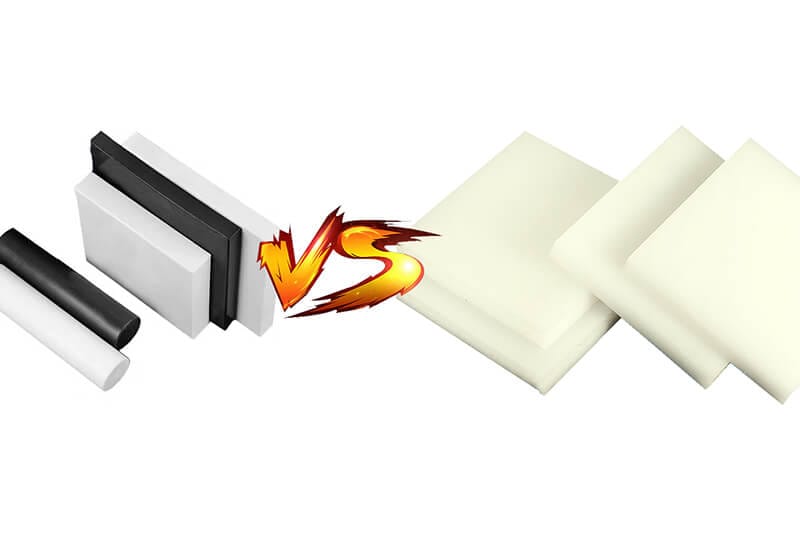
In the manufacturing industry, PVDF is famous for its use in biomedical membrane applications and wastewater treatment along with some other important purposes. On the contrary, PTFE is highly desirable to create a non-sticking layer while incorporating nonreactivity, hydrophobicity, and a low coefficient of friction.
While the two materials’ applications are nearly the same, it challenges the product designer’s skill in choosing the right material for producing the deliverables and the delivery of the next order completion. Therefore, having a comprehensive comparison between PVDF and PTFE is useful. The respective discussions in this article will answer which material is right for you.
Side-by-side Comparison: PVDF vs. PTFE
The following table will provide a brief comparative overview.
Criteria | PVDF | PTFE |
---|---|---|
Polar Functionality | Yes | No |
Physical properties | Colorless and transparent with a higher level of hardness, strength, and a high dielectric constant | White powder at room temperature with a low friction coefficient |
Wear resistance | Not applicable | High |
Electrical Insulation | Less than PTFE | Above average |
Cost | Money saving | Comparatively expensive |
Basics of PVDF
PVDF, also known as Polyvinylidene Fluoride, is a high-performance thermoplastic fluoropolymer. It is semicrystalline and has excellent mechanical and thermal properties.
Production Process
In its production process, the first task is to extract Vinylidene fluoride from the reaction of acetylene and hydrogen fluoride. Next, the VF2 monomer forms an emulsion that goes through polymerization in the presence of VF2 monomers forming PVDF chains.
The PVDF chains are then extracted, and after the water is removed and the material is dried, usable PVDF is generated.
Core Properties
Most Common Applications
Basics of PTFE
The complete form of PTFE is Polytetrafluoroethylene. It is a synthetic fluoropolymer. It is highly favored among manufacturing sectors that produce products with non-stick and high-temperature resistance properties.
Production Process
PTFE’s production process is more complex than PVDF. It also showcases some properties of thermoplastic polymers. In this case, at first, TFE Monomers are produced through the synthesis of calcium fluoride (Fluorospar), Sulphuric Acid and Chloroform. Next, the polymerization process takes place and the TFE monomers are transformed into PTFE.
It can be used for various parts manufacturing works through the application of methods like cold compression Molding, Sintering Process, Isostatic Molding, etc.
Core Properties
Most Common Applications
Critical Comparison between PVDF and PTFE
Here, we do a critical comparison between the considered construction materials in consideration of various variables.
1. Stickiness
PTFE is less sticky than PVDF. The coefficient of PVDF ranges from 0.2-0.4 D. Whereas, the coefficient of friction of PTFE is 0.05 to 0.10. Again, PVDF’s density is 1.8g/cm3 while the density of PTFE ranges from 2.1 to 2.3 g/cm3.
Also, experiments demonstrate that the sticky behavior of so-called associative polymers is controlled by the density of bonding structures. However, it contradicts the theoretical predictions. In short, in the case of ‘stickiness,’ PVDF is the winner.
2. Thermal Stability
The second variable is thermal stability. PTFE can withstand 260°C very easily and the general PVDF can withstand 150°C. However, some of its forms can withstand more than 400°C without dimension deformability. Here, the winner is PTFE as reaching 400°C is a very low number of occurrences.
3. UV and Weather Resistance
PVDF is more good in dealing with UV rays and weathering components. On the other hand, PTFE cannot withstand sunlight exposure for a longer period.
4. Processing
PVDF is easy to process by using methods like extrusion, injection molding, and compression molding. With a tight tolerance, the machine can produce a significant amount of items within a short time. Here, PTFE lags behind due to its slippery nature and very high melting point.
5. Cost
Depending on grade, PVDF’s per ton price ranges from $4,900 to $12,600. On the other hand, the per-ton price of PTFE is $12,600. So, it’s a tie.
Final Words
We expect that our elaboration on “Comparing PVDF and PTFE: Which Material is Right for You?” will help product designers, label designers, on-field professionals, and the whole company in choosing the suitable material.
Both materials serve similar purposes, but in two or three categories, one showed greater value than the other. This is the chosen point. The material should be chosen by aligning with the final product type.
If you don’t know how to choose the right material between PVDF and PTFE, contact UVTECO, who is a top supplier of both materials and machining services. I believe that UVTECO is a trustworthy partner for your project.
Related Blogs
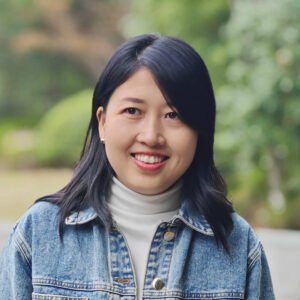
Looking for a trustworthy Supplier
Need a Trustworthy Supplier of Plastic, Foam, Sponge, Rubber, Metal, and Machining Solution. Click the Button, We Will Be In Touch With You As Quickly As Possible.